
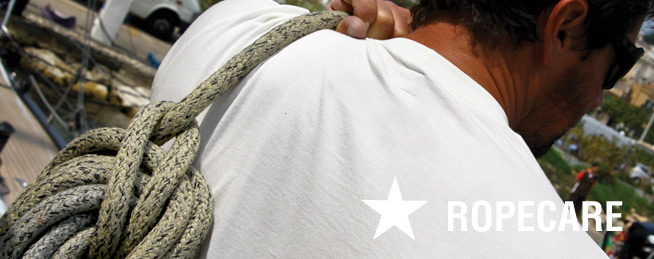
How to select a rope
Selecting the proper rope involves evaluating a combination of factors and that is not always so simple to do. Some of these factors are quite easy to compare based only on the rope specifications. Others are not easily quantified, such as a preference for a specific color or how a rope feels in your hand.
Reducing application factors that pertain to sizes or strengths on an initial purchase creates unnecessary frequent replacements and potentially dangerous conditions, in addition to increasing long-term costs. For fiber and construction that is equal, a larger rope will outlast a smaller rope because of the greater surface wear distribution. Similarly, a stronger rope will outlast a weaker one because it will be used at a lower percentage of its break strength with a reduced chance of it being overstressed.
Safety first
Maximizing the safety and rope performance begins with selecting the right rope, managing its strength loss through optimal handling practices, and retiring it from service before it creates a dangerous situation. Ropes when used properly they will give consistent and reliable service. The cost of replacing a rope is extremely small when compared to the physical damage or injury to personnel a worn out rope can cause.
Rope breaking loads
Because all ropes are terminated with a splice or a knot, all published strengths herein are based on our lab tests, under a very tight same protocol.
When comparing our breaking load values to other rope manufacturers, please be sure that you are comparing similar kind of ropes, using same fibers, approximately same diameters and weight/meter.
Normal working loads do not cover dynamic conditions such as shock loads or sustained loads, nor do they cover where life, limb or valuable property are involved. In these cases, a lower working load must be used.
A higher working load may be selected only with expert knowledge of conditions and professional estimates of risk, if the rope has been inspected and found to be in good condition, and if the rope has not been subject to dynamic loading (such as sudden drops, snubs, or pickups), excessive use, elevated temperatures, or extended periods under load.
Aggressions to a rope
Apart from weather all rope hardware such as sheaves, rollers, capstans, cleats and knots are, in varying degrees, damaging to the rope. It is important to understand that rope moves, and, even under ideal conditions, it loses strength during use in any application.
Any sharp bend in a rope under load decreases its strength substantially and may cause premature damage or failure.
In sizing the radius of bitts, fairleads, and chocks for best performance the following guidelines are offered. The diameter of the surface should be at least three times the rope's diameter.
A 4-to-1 ratio would be better yet because the durability of the rope increases substantially as the diameter of the surface over which it is worked increase.
The ratio of the length of an eye splice to the diameter of the object over which the eye is to be placed (bollard, bitt, cleat, etc.) should be a minimum 3-to-1 relationship, and preferably 5-to-1.
Knots - not the rope´s best friends
Presence of knots can reduce tensile strength by over 50%. In order to preserve the properties of the product and to avoid premature failures the working load must never exceed 25% of the breaking loads shown. It is vital that the reduction in strength by the use of knots be taken into account when determining the size and strength of a rope to be used in an application. To avoid knot strength reduction, it is recommended that a rope be spliced according to the manufacturer’s instructions. Splice terminations are used in all our ropes to determine new and unused tensile strengths.
Therefore, whenever possible, spliced terminations should be used to maximize the rope strength for new and used ropes.
Ropes and sheaves – balance is important
To assure maximum efficiency and safety, sheaves for braided ropes should be no less than eight times the rope diameter. The sheave groove diameter should be no less than ten percent greater than the rope diameter. The sheave groove should be round in shape.
Sheaves with “V” shaped grooves should be avoided, as they tend to pinch and damage the rope through excessive friction and crushing of the rope fibers. Sheave surfaces should be kept smooth, and free of burrs and gouges. Bearings should be maintained to ensure smooth rotation of sheaves.
How to store a rope
All rope should be stored in a clean, dry area, out of direct sunlight, and away from extreme heat. It should be kept off the floor and on racks to provide ventilation underneath. Some synthetic rope, in particular polypropylene, may be severely weakened by prolonged exposure to ultraviolet rays. UV degradation is indicated by discoloration and the presence of splinters and slivers on the surface of the rope.
It is the right time to change the rope?
Unfortunately, there are no definitive rules nor are there industry guidelines to establish when a rope should be retired because there are so many variables that affect rope strength. Factors like load history, bending radius, abrasion, chemical exposure or some combination of those factors, make retirement decisions difficult. Inspecting your rope should be a continuous process of observation before, during, and after each use. In synthetic fiber ropes, the amount of strength loss due to abrasion and/or flexing is directly related to the amount of broken fiber in the rope’s cross section. After each use, look and feel along every inch of the rope length inspecting for abrasion, glossy or glazed areas, inconsistent diameter, discoloration, and inconsistencies in texture and stiffness.